

Therefore, a surface optical diffuser, manufactured by an optical process, is more effective in display applications. Optical processes are less expensive than mechanical ones, and a surface-relief diffuser is more easily mass produced than a volume one. Its design and manufacture are more complicated than the non-holographic method and are beyond the scope of this works since its function far exceeds that required for aforementioned applications. Such a diffuser exhibits controllable scattering angles, aspect ratio, position of the scattering lobe, and multiple scattering lobes. The holographic diffuser is essentially based on the holographic recording of a speckle pattern generated by an optical system that contains conventional diffusers. Research in more advanced diffuser, called the “holographic diffuser” is reported in the literature. However, POC did not provide any details concerning the patterns molded on the surface, and the elucidating of the diffraction physics is difficult. Recently, a research team at the Physical Optical Corporation (POC) proposed surface-relief holographic optical elements, named light-shaping diffusers.

Design and control are easy, but mass production is difficult since the duplication of volume diffusers is not trivial. The third method implants shaped particles by recording speckles in a phase volume holographic medium. Mass production is also difficult and expensive.
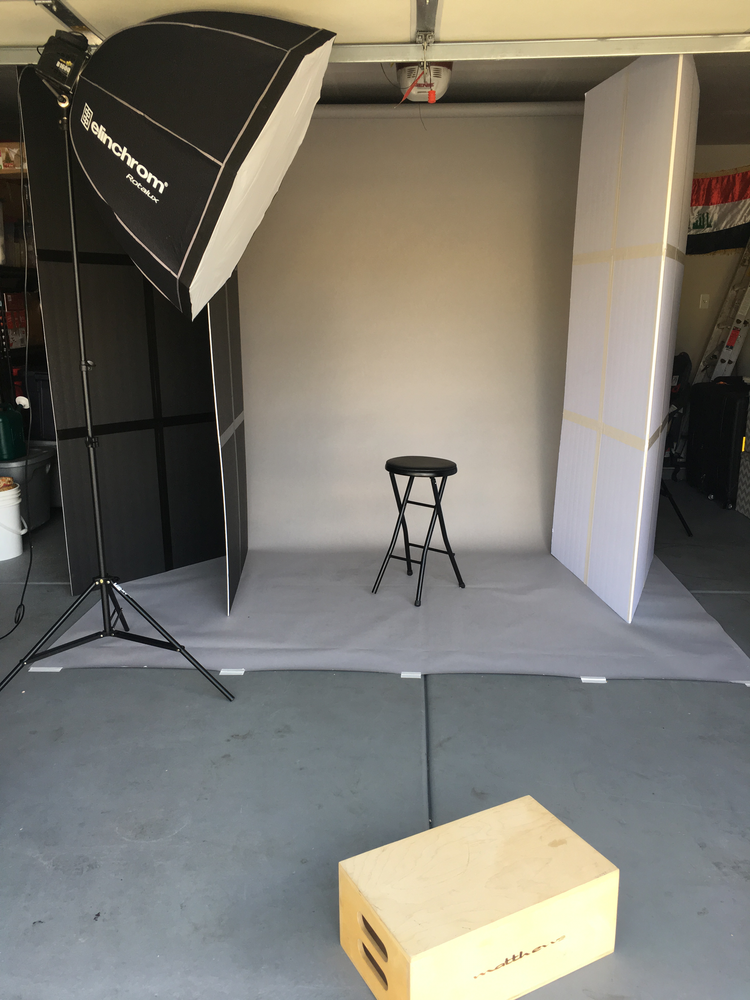
Designing and controlling the aspect ratio of a scattering pattern are difficult. The second method creates high-density dies to mark mechanically a metal surface.
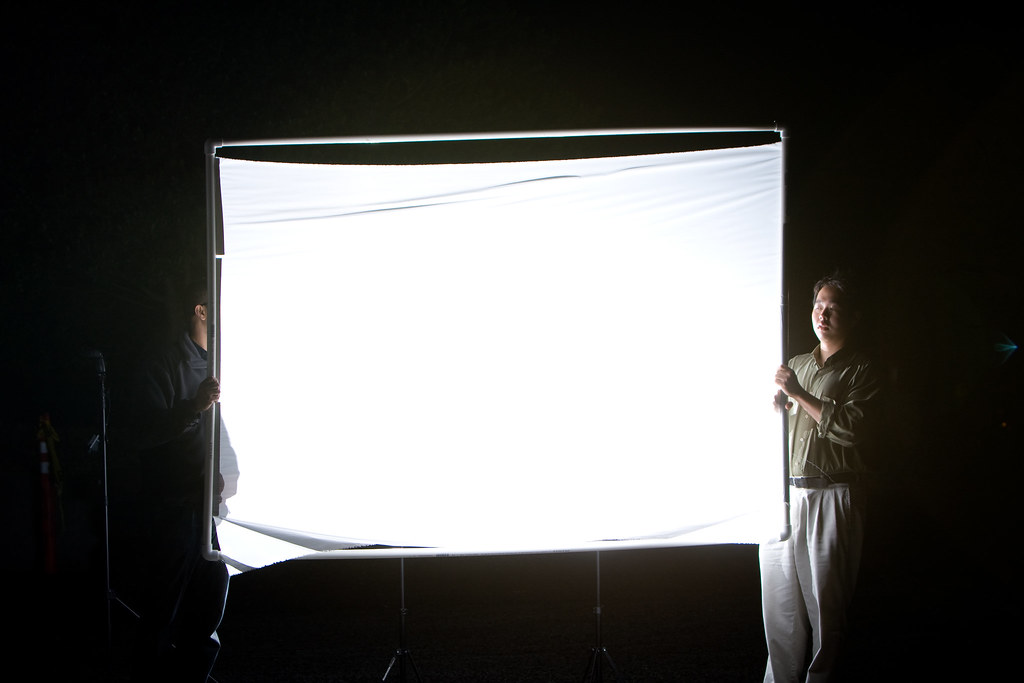
However, this method is limited by the Morie patterns (seen as wavy dark bands) that are formed by the beating of the lenticular structure pitch and the displaying pixel. The Fresnel lens collimates incident light and the lenticular structure then expands the light in particular dimension. The first method uses a Fresnel lens combined with a lenticular structure for rear projection. In the literature, many optical methods for fabricating a special diffuser that can diffuse light into a specific area have been reported. Light with circular cross-section is diffused into circular pattern by circular granules and into elliptical pattern by elliptical granules. Conceptually, if a diffuser’s granules can be made elliptical (like an American football) rather than circular (like a baseball), then the incident beam will be diffused into an appropriate pattern, schematically shown in Fig. If a diffuser forms an image in a more spatially selective manner, then that image will appear brighter and the diffuser is said to have gain. The shortcoming of a conventional diffuser in such applications is that it wastefully illuminates the useless area. For example, in a conference room, the illumination of a projection display must be concentrated in a specific area, where viewers are gathered, rather than scattered over a wide area. However, the circular spreading is not suitable for certain applications. Light that passes through a surface with a random granular pattern spreads circularly and is suitable for applications in theaters where the required vertical-view-angle is as wide as the horizontal-view-angle. In recent years, ground glass diffusers have been used as light-homogenizing devices in LED display panels, and LCD backlights, as well as beam-homogenizing devices. Another popular application is the projection screen of front and rear projectors. The most common daily application of ground glass is the lamp mask, which can soften the harsh light from a lamp bulb. Ground glass has a random granular surface, and thus functions as a Lambertian diffuser that can uniformly redistribute incident light. The pattern of light diffused from a random granular surface spreads uniformly. The pattern of light scattered from a periodic surface is periodic. Light can be scattered into special patterns from a rough surface, which can be classified into surfaces with periodic and those with random profiles.
